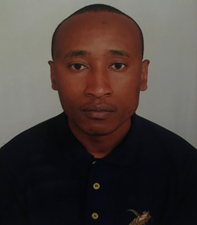
Billy Mwangi is a registered graduate mechanical engineer with experience in maintenance management, project management, process control and change management. He has been involved in projects that have reduced CO2 emission and the carbon footprint in Kenya. Also; he has been engaged in biomass waste conversion to green energy sources and industrial investment grade energy audits.
Billy is passionate on energy management, project management, renewable and sustainable energy, environment and climate change. He is enthusiastic about steam boilers and distribution systems, compressed air systems (CAS), fluid flow systems, Heating Ventilation and Air Conditioning (HVAC) and refrigeration systems, Non Destructive techniques (NDT) and research.
Special keenness on management of industrial energy cost comes from his passion to continually manage and reduce cost so as to improve product profitability. He derives endless satisfaction in managing industrial energy cost.
Billy’s spare time is spent with family, mountaineering, swimming, playing chess and football, reading novels and watching movies.
Reg. No: F56/12293/2018.
Waste Heat Recovery From Boiler Stacks.
Steam is generated in pressured vessels called boilers. The cost to industry to generate steam is substantial, typically up to 40% of total expenditure. Therefore, boilers should be operated at high efficiency. Most of the heat loss from the boilers occurs through stack flue gases; accounting for up to 30% of the total energy input into the boiler.
For large boilers and those that use natural gas, economizers and air – preheaters are installed to recover waste heat from flue gases. However, these heat exchangers are not suited for small capacity boilers and also those that use Heavy Fuel Oil (HFO). Most small boilers do not recover waste heat from flue gases and therefore loose significant energy through flue gases to the environment. The thermal efficiency of boilers is exclusively a function of heat loss especially through hot flue gases rejected and dumped to the environment at high temperatures.
This project was conducted in two parts; the first being to quantify these loses for ten industrial boilers. The second part of this project involved fabrication of a laboratory stack to accommodate modifications so as to recover waste heat from flue gases. To recover some of the waste heat the laboratory stack was modified to act as a double pipe coil heat exchanger to recover waste heat from the same flue gases. The modification involved brazing a helical 9.53mm (3/8inch) copper tube with a 101.6mm (4 inch) pitch on the external surface of a 4 inch diameter pipe and 1280 mm height model stack. The assembly was then insulated with 35.3mm fiberglass insulation.
The flue gases were conveyed in the normal way but lost heat to the water flowing in the copper tube. It was found that upto 74% of the waste heat is lost by flue gases through the laboratory model stack surface and upto 83% by the industrial boiler stack surface. It was also found that about 30.6% of the waste heat energy contained in flue gas was recovered by the laboratory model stack by employing the double coil heat exchanger. This project has therefore shown that a significant amount of waste heat from small capacity boilers can be recovered with some limited modifications on the boiler stacks.
Research Supervisors: